Observatoire Canadien de l'Hydrogène : observer,…
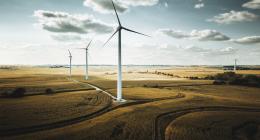
Au cœur de la stratégie de réduction des émissions de gaz à effet de serre des pays, l’électromobilité s’annonce comme une véritable révolution pour le paysage industriel mondial, et donc Européen.
Au cœur de la stratégie de réduction des émissions de gaz à effet de serre des pays, l’électromobilité s’annonce comme une véritable révolution pour le paysage industriel mondial, et donc Européen. Composant essentiel, la batterie porte de grands enjeux que Sia Partners se propose d’analyser au cours d’une série d’articles : une présentation du marché de la batterie électrique et des différents types d’investissements qui y sont liés, puis l’intérêt qu’a l’Europe à développer cette filière – au-delà de la simple captation de valeur d’une industrie prometteuse – et finalement sous quelle forme ce nouvel écosystème industriel pourrait s’articuler et se structurer pour les années à venir.
En novembre 2019, Tesla a annoncé que sa future gigafactory européenne serait installée dans la banlieue de Berlin. Le complexe colossal, d’un investissement estimé de 4 Mds d’euros, assemblera les Model Y et Model 3 de la marque et, mieux encore, produira directement les batteries qui contiendront l’énergie stockée dans les véhicules. Ces dernières représentent 40% de la valeur d’un véhicule électrique, c’est un composant stratégique encore peu maîtrisé en Europe où la filière reste pour le moment timide face aux géants asiatiques et à l’américain Tesla. Les applications sont pourtant très diverses – stockage d’énergie, automobile, électronique, outillage industriel … - il convient donc d’en sécuriser l’approvisionnement.
Quels sont les investissements possibles permettant de sécuriser l’approvisionnement en batteries électriques ?
Au fil de cet article, nous présenterons dans un premier temps le marché des batteries électriques et dans quelle mesure le développement de la mobilité électrique ce façonnera ce marché dans le futur. Ensuite, nous nous pencherons sur la chaine de valeur de la batterie lithium-ion, en illustrant avec quelques exemples les investissements réalisés sur les différents maillons de cette chaine pour sécuriser l’approvisionnement des batteries dans le monde et en Europe. Nous terminerons par quelques exemples de technologies de ruptures qui pourraient bouleverser le marché des batteries sur le long terme.
Le marché des batteries électriques tous types confondu représente 80 Mds de dollars en 2018 et augmente de 9% par an depuis 2010. Deux types de technologies dominent le marché mondial: la batterie au plomb, qui représente le plus gros volume de la production et la batterie lithium-ion qui jouit de la plus forte croissance. Ces deux types de batteries se partageaient le plus gros du marché en valeur en 2018 : 40 Mds de dollars pour les batteries au plomb et 37,5 Mds de dollars pour les batteries lithium-ion.
Aujourd’hui, la presque totalité de la production de cellules pour les batteries lithium-ion se situe en Chine, au Japon et en Corée du Sud. En 2018, moins de 3% des batteries sont produites en dehors de ces trois pays, et environ 1% de la production est européenne. Il est partagé entre une multitude d’acteurs dont les six plus importants – LG Chem, Samsung SDI, Tesla, Panasonic, CATL et BYD – représentent en cumulé en valeur 45%.
Pour exprimer le marché en volume, il convient de définir de quelle manière mesurer la production d’un site industriel. La capacité d’une batterie s’exprime en kWh (kilo Watt heure), ce qui correspond à l’énergie maximale qu’elle est capable de stocker. La production d’une usine de batterie s’exprime ainsi en GWh (Giga Watt heure) par an et correspond à la somme des capacités des batteries produites par l’usine en une année. La production mondiale en 2018 était respectivement de 420 GWh pour les batteries au plomb et de 160GWh pour les batteries lithium-ion.
Le premier consommateur de batteries au monde est l’automobile. Dès Janvier 2019, la valeur mondiale des investissements annoncés par les constructeurs automobiles dans le développement et la production de véhicules électriques et hybrides atteint 300 Mds de dollars, dont 224 Mds pour la seule période 2019-2020. La plupart des constructeurs investissent principalement sur leur sol d’origine et un peu en Chine, excepté les constructeurs allemands qui allouent la moitié de leurs investissements à la Chine :
Illustration 1 : Investissement réalisés par les constructeurs automobiles dans les véhicules électriques dans chaque pays, par pays d’origine des constructeurs, en Mds d’euros (source : Avicenne)
En 2018, les ventes mondiales de véhicules électriques et hybrides ont atteint les 1,26 millions d’unités, dont 769 000 en Chine. Sur les 96 millions de voitures vendues sur l’année, cela ne représente qu’une part de 1,3%, mais cette part est estimée atteindre 48% en 2030. Le cabinet McKinsey estime qu’en 2040, 70% des nouvelles immatriculations en Europe seront des véhicules 100% électriques, alors que certains pays européens ont même annoncé bannir les véhicules thermiques d’ici 2030 ou 2040. Cela impliquera une explosion de la demande en batteries.
Illustration 2 : Estimation du marché des véhicules en 2030. Source : The Future of Battery Production for Electric Vehicles, BCG.
Le site Automobile Propre répertorie 188 modèles de véhicules hybrides ou 100% électrique de 45 constructeurs, ce qui n’inclut pas les nombreux constructeurs Chinois. La répartition entre véhicules hybrides et électriques est pour le moment 50/50. Pour 110 modèles, l’information du type de batterie est incluse et montre que la batterie lithium-ion domine la mobilité électrique :
Illustration 3 : Nombre de modèles de véhicules électriques par type de batteries. Source fiche d’identité des véhicules : https://www.automobile-propre.com/voitures
La position dominante de la batterie lithium-ion sur le marché de l’automobile électrique devient alors motrice de l’évolution du marché des batteries électriques.
Il est estimé que le marché de la batterie au plomb sera de 57 Mds de dollars en 2030, contre 110 Mds de dollars pour la batterie lithium-ion.
La production mondiale des batteries lithium-ion était de 160GWh en 2018. Elle passera à 500GWh en 2025 et atteindra 1200GWh en 2030. Le secteur de la mobilité électrique représente 66% de ces batteries, soit une production de 106GWh. En 2030, il est attendu une production mondiale de batteries lithium-ion est de 1200GWh et, dans le même temps, une part de la mobilité électrique passée à 85% soit une production de 1020GWh.
Pour multiplier par presque 8 la production mondiale de batteries lithium-ion et baisser significativement les coûts de production, il s’avèrera nécessaire de jouer au gigantisme, ce que les industriels font grâce au modèle des gigafactories, que nous aborderons plus loin dans cet article. Plus encore, c’est bien l’ensemble de la chaine de valeur qui est impactée par l’explosion de la demande des batteries.
La batterie électrique est un objet complexe. Les différentes étapes de sa chaine de valeur sont fortement liées entre elles par la part importante que chaque étape représente dans le coût de l’étape suivante :
Illustration 4 : Chaine de valeur de la batterie électrique : où se situe la valeur ?
De façon à garantir la survie de la filière automobile, il est important de continuer de capturer une forte partie de la valeur des automobiles. Dans un véhicule électrique (BEV), 40% de la valeur est issue de la batterie, et le reste de la traction 10% – bien plus que toute la chaine de traction d’un véhicule thermique (16%). Maîtriser la fabrication des matériaux actifs et des batteries donne un pouvoir certain sur le marché de la mobilité électrique.
Les batteries sont donc l’élément essentiel et central de la conception du véhicule électrique, et si la majorité des constructeurs automobiles externalisent la production des cellules unitaires des batteries, ils internalisent l’assemblage de ces modules en packs. Cela leur permet de contrôler la manière dont l’espace disponible dans les véhicules est occupé, ce qui a un impact direct sur l’autonomie et le taux de charge des véhicules, ainsi que sur la manière dont les batteries pourront être refroidies. Elles sont donc de plus en plus co-conçues par le fabriquant de batteries et le constructeur automobile afin de gagner en personnalisation et en rapidité de mise en production, ce qui n’est possible que via un rapprochement entre constructeurs automobiles et producteurs de batteries.
Les matériaux principalement présents dans la composition des batteries lithium-ion sont le lithium, le cobalt, le nickel, le graphite, ainsi que d’autres terres rares. Suivant la demande en batteries, la demande de ces matières premières augmentera de manière exponentielle. Néanmoins, la forte volatilité des prix à court et moyen terme, la structure rigide de la chaine d’approvisionnement et le manque de diversification de l’offre rendent la demande future des matières premières difficile à prédire. Sur le long terme, l’amélioration de l’efficacité de l’emploi des ressources et les changements de technologie pourraient permettre de réduire la demande de certains matériaux.
Illustration 5 : Demande et part de la production mondiale en matières premières pour les batteries électriques. Source : COMMISSION STAFF WORKING DOCUMENT Report on Raw Materials for Battery Applications, Figure 16 Metals demand for rechargeable batteries
Aujourd’hui, seulement quelques pays détiennent la production de ces matières premières, dont certains pèsent très lourd dans les exportations.
Illustration 6 : production minière et part de la production mondiale des principaux pays producteurs de matières premières pour les batteries électriques. Source : COMMISSION STAFF WORKING DOCUMENT Report on Raw Materials for Battery Applications. Carte créée via mapchart.net ©
Environ la moitié des réserves de lithium se situent en Amérique du Sud. Pourtant, la Chine possède la majorité des unités de raffinage de lithium, ce qui consolide sa position dominante sur le marché des batteries lithium-ion.
Sécuriser ces approvisionnements est donc un enjeu de taille. Pour ce faire, les groupes européens investissent dans les pays producteurs afin d’exploiter directement les gisements. Le groupe minier et métallurgiste français Eramet a découvert un gisement de lithium en Argentine renfermant des ressources estimées à 9 millions de tonnes, soit un siècle d’exploitation. L’objectif est, à horizon 2025, que le site produise la moitié du besoin de l’Europe en lithium – 24000 tonnes par ans. Néanmoins, les risques politiques et monétaires ont fait hésiter la direction du groupe avant de se lancer dans le projet d’un montant de 525 millions d’euros.
D’autres groupes préfèrent donc investir dans l’exploitation des ressources européennes, bien que moins de 1% des ressources de lithium seraient dans l’Union Européenne, et 3% en Serbie. Le Labex Voltaire a recensé 39 projets significatifs et gisements ainsi que 15 compagnies d’exploration ou d’exploitation qui ont conduit à la création de projets miniers dans plusieurs pays d’Europe. Par exemple au Portugal, premier producteur européen de lithium (400 tonnes produites en 2017), l’investissement cumulé dans les cinq zones les plus attractives pour les compagnies minières est estimé à un potentiel de 3,3 Mds d’euros.
La demande en matériaux actifs pour les cathodes de batteries lithium-Ion est passée de 67 000 tonnes en 2010 à plus de 345 000 tonnes en 2018. En 2030 il est attendu 1,67 millions de tonnes et les applications lourdes type véhicule électrique compteront pour 98% de la demande contre 89% aujourd’hui (2018). Dans le même temps, le coût des matériaux actifs par batterie par kWh produit a chuté ces dernières années : de 400$ environ en 2010, on est passé à 150$ en 2018, et il est estimé à 120$ en 2025.
Cette augmentation exponentielle de la demande en matières premières et en matériaux actifs correspond à la mise en place de nouveaux sites industriels de production de batteries – les gigafactories.
Nous l’avons vu, la demande en batteries augmentera de manière spectaculaire pour passer, dans le cas des batteries lithium-ion, de 160GWh produits en 2018 à 1200GWh produits en 2030. Cette production est principalement tirée par le secteur de la mobilité électrique.
Tesla et Panasonic ont alors initié le modèle des gigafactories, des usines géantes permettant de réaliser des économies d’échelles remarquables. Il est en effet estimé qu’un site ne peut réaliser des économies d’échelles suffisantes qu’à partir d’une production annuelle d’environ 10 GWh selon le BCG, ce qui est nettement supérieur aux unités de production actuelles (de l’ordre de quelques dizaines de kWh par an) et permet d’équiper environ 150 000 véhicules électriques. McKinsey estime qu’à partir de 8GWh produits par an, la productivité par rapport à un site plus petit ou sous-utilisé est doublée. Un tel site de production nécessite 5 à 7 ans pour sortir de terre en partant de zéro.
Comparer une gigafactory à un site de production classique de batteries permet de se rendre compte du gigantisme de ces sites industriels :
Illustration 7 : Comparaison entre un site de production classique de batteries électriques et une gigafactory.
La gigafactory de Tesla et Panasonic dans le Nevada a de fait une capacité de production de 35GWh par an, qui sera en 2020 relevée à 50GWh par an.
Les constructeurs asiatiques annoncent de leur côté de nombreux projets de gigafactory. C’est le cas de BYD qui ouvrira une usine de 24GWh (60 GWh à terme) à Quihai, au plus près du plus grand site de production chinois de lithium (83% de la production de lithium chinois). Le Coréen SK Innovation souhaite vouloir produire 55GWh en 2022 dans ses usines coréennes, contre 4,7GWh actuellement. Néanmoins, cette augmentation brutale de la capacité de production fait qu’il est estimé par le BCG que 40% de la production mondiale en batteries en 2021 serait inutilisée.
Les projets de gigafactories foisonnent et sur plus de 70 projets recensés en 2018, 46 seraient sur le sol Chinois, qui possède déjà la majeure partie de la production actuelle. En Europe cependant, la demande en batterie projetée en 2040 (1200 GWh par an) est 5 fois supérieure au volume de production des projets annoncés (en 2018) par Northvolt (Suède), LG Chem (Pologne), Samsung SDI (Hongrie) et CATL (Allemagne). Cette demande qui nécessiterait 80 gigafactories de 15GWh par an soit un investissement de 150 Mds d’euros. Faute d’investissements suffisant, l’Europe sera contrainte d’importer les batteries manquantes, ce qui lui fera perdre cette création de valeur et rendra moins certaine l’approvisionnement - un risque supplémentaire sur son industrie.
Les pays européens doivent donc convaincre les industriels et les investisseurs d’ouvrir leurs usines chez eux. Dans le cas de la future gigafactory de Tesla à Berlin, trois arguments sont identifiés : la renommée de l’ingénierie allemande ; la présence de clients – les constructeurs automobiles allemands – réalisant de grand efforts dans l’électrification ; la stabilité du pays et l’accès au marché unique, le Royaume-Uni ayant été écarté à cause de l’éventuel Brexit. Ces points mettent en avant le besoin pour les industriels de s’implanter dans des régions où le marché est certain.
La complexité de la règlementation européenne est néanmoins une des raisons du retrait de l’Europe de certains acteurs non européens de l’automobile.
Le gigantisme n’est pas la seule solution permettant une réduction des coûts de production.
Les gigafactories étant de fait des usines neuves, elles bénéficient des innovations récentes (Maintenance prédictive, Material-Based Processing, paramétrage des machines intelligent, contrôle qualité intelligent …) qui permettraient une réduction des coûts de production jusqu’à 20% et une augmentation de la densité énergétique des batteries de 10 à 15%. De plus, la modularité de la production permet de produire très rapidement de nouveaux modèles en paramétrant ses appareils selon les spécifications demandées par les clients.
A contrario, le coût du travail représente une faible proportion du coût des batteries, rendant de fait la délocalisation peu intéressante pour baisser les coûts. De plus, cela augmenterait la complexité de la chaine d’approvisionnement.
De nouvelles générations de batteries permettraient aussi de réduire ces coûts. Il s’agit de la voie actuellement privilégiée par les producteurs de batteries. Ces futures technologies seront abordées plus loin dans cet article.
Maroš Šefovi, vice-président de la commission européenne, souhaite que les batteries européennes soient vertes donc éco-conçues – de l’extraction des minerais au recyclage – pour réduire l’empreinte carbone de la filière. Le constructeur BMW a par ailleurs annoncé vouloir s’orienter dès 2020 vers un approvisionnement plus responsable sur les plans sociétaux et environnementaux et se tourner entre autres vers le recyclage. Ce dernier permet également de limiter la dépendance aux pays tiers et une potentielle baisse des coûts globaux de la filière.
Les batteries peuvent être reconditionnées dans des applications qui, contrairement au véhicule électrique, peuvent se permettre une capacité dégradée – par exemple les outillages industriels. Mieux encore, elles peuvent être recyclées afin de récupérer leurs matériaux, qui pourront, selon la qualité du procédé, resservir à fabriquer des batteries ou être réutilisés dans d’autres industries ou dans la sidérurgie.
C’est principalement le cobalt qui est récupéré au cours du processus, atteignant alors un prix plus faible que s’il était issu d’un gisement. Cela permettrait d’approvisionner 10 000 tonnes de cobalt par an à moyen terme en Europe, soit 65% de la demande de l’industrie Européenne actuelle. Mais aujourd’hui, le recyclage du graphite, lui, est limité car il est souvent perdu au cours du processus. Les terres rares comme le cérium et le lanthane ont un taux de recyclage de seulement 1%.
Développer le recyclage pourrait donc être un moyen de pallier aux les difficultés liées à l’approvisionnement en matières premières. Les constructeurs automobiles européens en sont conscients et investissent dans ce secteur, en association avec des spécialistes, d’autant que ce secteur est éligible à des subventions des états. Grand View Research estime que le marché mondial du recyclage des batteries de véhicules électriques passera de 8 Mds de dollars en 2016 à plus de 21 Mds de dollars en 2025.
Néanmoins, la collecte des batteries est un point dur à lever pour la mise en place d’une véritable filière du recyclage. Un nombre significatif de véhicules y compris électriques démarrent en fin d’utilisation une seconde vie dans des pays hors Europe, ce qui limite de fait la récupération des batteries. Un mode de commercialisation plus centré client a été mis en place par Fiat et Renault: louer les batteries au lieu de les vendre avec le véhicule.
De plus, le marché du véhicule électrique étant encore récent - en particulier en Europe - et puisque la durée de vie estimée d’une batterie est de 10 ans, un grand nombre de véhicules ne sera donc pas encore arrivé en fin de vie. Cette durée de vie fixe permet tout de même à la filière du recyclage de se préparer en amont et d’anticiper le besoin en recyclage.
Les batteries lithium-ion ont été mises au point par Sony Energitech en 1991, ce qui témoigne d’un délai de mise sur le marché de l’ordre de la dizaine d’année pour ce type de produits. Une rupture technologique demandera une dizaine d’année pour arriver à une maturité suffisante afin de supplanter la batterie lithium-ion dans une production de masse.
Une nouvelle génération de cellules lithium-ion se base sur la technologie de l’électrolyte solide, dont la densité énergétique est supérieure à 400Wh/kg (contre 230Wh/kg pour les batteries lithium-ion actuelles) et dont le chargement est plus rapide. La maîtrise de cette technologie en interne ou dans sa filière de sous-traitants est fondamentale pour la compétitivité des constructeurs automobiles dans le futur, puisqu’elle permettrait de proposer à un meilleur prix un véhicule aux performances supérieures. Pour BMW par exemple, utiliser cette technologie est encore prématuré à ce jour, mais le constructeur allemand espère profiter de cette avancée technologique pour ses modèles de 2030. Toyota et Lexus espèrent eux proposer cette avancée technologique dès le milieu de la décennie 2020.
En Chine, la startup Qing Tao Energy Development a ouvert un premier site de production de batteries à électrolyte solide de 0,1 GWh par an à Kunshan, pour un investissement de 126 millions d’euros, avec une capacité de production prévue de 0,7 GWh par an en 2020. Ces batteries serviront dans un premier temps dans des équipements spéciaux et des produits à haute valeur ajoutée, mais des discussions sont en cours avec des partenaires de l’industrie automobile.
En Europe, Saft (filiale de Total) a établi une alliance avec entre autres Solvay, Manz et Siemens pour développer cette technologie sur le sol Européen. L’alliance compte également s’associer avec des établissements d’enseignement supérieur, des centres de recherche et des PME spécialisées dans le domaine. Le programme de recherche, de développement et d’industrialisation durera 7 ans. L’industrialisation se ferait sous forme de blocs évolutifs d’une capacité de 1GWh.
Dans un futur plus lointain, des ruptures technologiques permettraient de pallier les difficultés liées à l’approvisionnement en utilisant d’autres matières premières ou améliorer les performances en temps de recharge ou en densité énergétique. Ces futures générations de batteries ne sont pas encore suffisamment matures à ce jour, mais elles permettraient de baisser les coûts et donc d’augmenter l’attractivité de la mobilité électrique. En voici quelques exemples.
Les batteries Sodium-Ion permettrait, pour un coût équivalent aux batteries lithium-ion, un temps de recharge de quelques minutes seulement et un nombre de cycles de recharges dix fois plus important. Elles utilisent des matières premières bien plus abondantes – sodium, aluminium, hard charbon. La startup française Tiamat veut établir un démonstrateur industriel de 10 à 20 MWh. Le projet de 25 millions d’euros est fortement convoité par l’Asie et les Etats-Unis, et le constructeur PSA pourrait être l’un des investisseurs. La densité énergétique est pour le moment de seulement 120kWh/kg, mais ses cibles sont aussi bien dans les robots industriels que la mobilité électrique y compris les véhicules particuliers. La startup ambitionne ensuite de créer ses propres gigafatories de plusieurs GWh en 2021 ou 2022.
Le projet Européen LISA, d’un budget de 7,0 million d’euros, cherche quant à lui à développer des batteries lithium souffre, car celles-ci ne nécessitent pas de matières premières « critiques », sont plus légères et pourraient avoir une densité énergétique dix fois supérieure aux batteries lithium-ion.
Pour créer une filière industrielle intégrée (chaîne de valeur et d'approvisionnement) des batteries automobiles en Europe, il faut saisir la chance de croissance exponentielle du marché des véhicules électriques. Ceci passe par des investissements dans la production des matières premières, la construction de gigafactories produisant les batteries des véhicules et la mise en place d’une véritable filière du recyclage.
Le développement de nouvelles technologies et leur adoption par les constructeurs automobiles sont longs, de l’ordre de la quinzaine d’années. Par conséquent, investir aujourd’hui dans les technologies de batteries lithium-ion de deuxième génération dans l’automobile est pertinent pour développer la filière.
L’Europe est la terre d’origine de certains des plus grands constructeurs automobiles, mais accuse en revanche un retard sur la production du composant phare du véhicule de demain. Plusieurs projets d’ « Airbus des batteries » se proposent pour répondre au besoin de création d’une filière européenne des batteries, et créer ainsi une recherche plus robuste et des synergies entre les maillons de la chaîne de valeur. Ce projet s'avère essentiel à la sauvegarde de l’écosystème industriel du vieux continent.